Oyu Tolgoi LLC today celebrated the completion of Shaft 2 of the world-class OT underground project, which is a significant milestone for the project.
The ceremony was attended by national contractors who were crucial for the development of one of the world’s largest and most modern shafts project and other key stakeholders.
In special remarks delivered at the celebration event by Ambassador Batsukh Galsan, Chairman of the Board of Directors of Oyu Tolgoi LLC, highlighted the great support provided by the Government of Mongolia for this remarkable achievement, which increases Mongolia’s global competitiveness in terms of the mining and technology development.
Armando Torres, Chief Executive Officer of Oyu Tolgoi LLC said, “Shaft 2 construction – from sinking through to equipping – has taken three years and four months in total. Close to 50 national companies and 2,500 people worked safely on Shaft 2 for approximately 2.6 million hours to complete this critical and complex piece of infrastructure that will accelerate the underground development of our Oyu Tolgoi mine”.
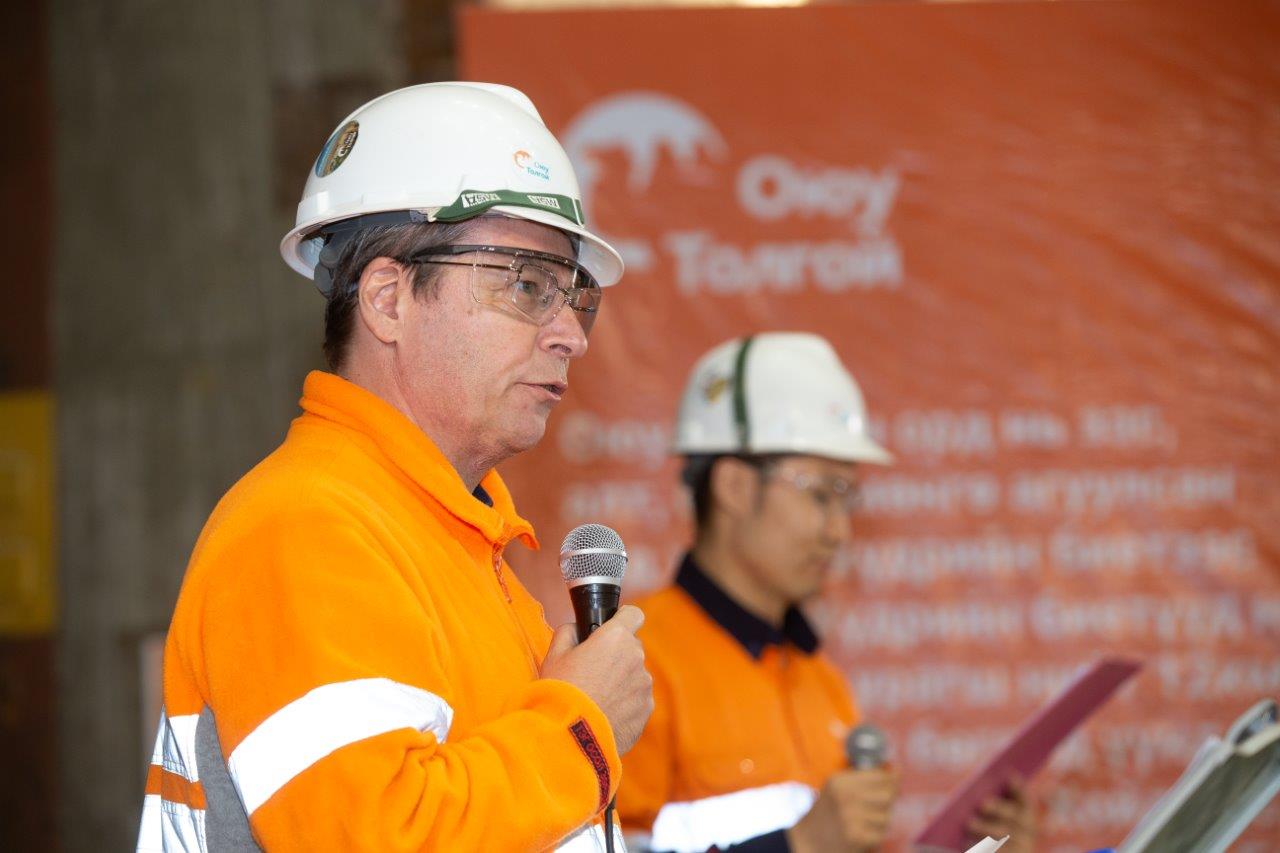
Shaft 2 with a depth of 1,284 metres is the main production shaft and primary access point for people and materials and provides infrastructure for the materials handling system in the underground mine. Its production hoist is the largest Koepe (Friction) rope hoist system in the world with two 60 tonne capacity skips capable of hoisting 28,000 tonnes of ore per day at a maximum speed of 59km/hr. Shaft 2 can carry 300 people per cage cycle versus a maximum of 60 people per cage cycle through Shaft 1. Shaft 2’s hoist rope-up process took 23 days by a team of approximately 500 people – one of the safest and most efficient rope-ups undertaken anywhere in the world.
Shaft 2’s role in the underground project
Once Shaft 2 is fully commissioned and receives state licensing, it enables the following two important steps forward for the underground mine:
- additional crews, materials and equipment to be transported and operate underground
- more rock to be removed from underground to enable further development and access to the ore body
From this point, the number of people working underground will no longer be constrained by the Service lift capacity of Shaft 1, but rather by volume of air moving through the underground via the existing ventilation (shafts 1, 2 and 5). Additional ventilation capacity is under construction with two more ventilation shafts – shaft 3 (intake) and 4 (exhaust). Currently, 700 people are able to work underground per shift.
Note for editors:
- Shaft 2 size comparison: 1,300m total (96m headframe and 1,284m underground) (equivalent to 15 Shangri-La Ulaanbaatar towers in total height – 14 below ground and one above ground). The inside diameter is 10m.
- Shaft 2 headframe which is 96m above surface is approximately the height of the Statue of Liberty (92m from base of pedestal to top of torch).
- Shaft 2 production hoist is the largest Koepe (Friction) rope hoist system in the world. The system uses:
- Two of the world’s largest Koepe winders
- 32 kilometres of steel ropes (approximately the distance between Oyu Tolgoi site and Khanbogd)
- Service hoist: 300 people at a time (maximum cage capacity) and approximately 2,400 people per day via a two and a half (2.5) minute journey. Maximum payload for cage is 48 tonnes at 10m/s (36km/hr).
- Production hoist: 2x 60 tonne capacity skips capable of hoisting 28,000 tonnes of ore per day at a maximum speed of 16.38m/s (59km/hr).
Overview of Oyu Tolgoi shafts:
Oyu Tolgoi has five shafts in total with Shaft 1 being currently operational providing access to underground project area for people and materials. Shafts 3 and 4 are currently under construction with a depth of 1,148m and 1,149m, respectively. Both shafts will provide additional ventilation (intake and exhaust) to support life of mine operations. Shaft 5 is currently operational with a depth of 1,174m allowing ventilation capacity two-fold enabling increase in lateral development and underground construction capability. Mine Dry named ‘Chandmani Operations and Service Centre’ was also completed in August 2019. Mine dry is the central coordination area of the underground operation including control rooms, wash, changing and PPE facilities, meetings rooms and offices.
Leave a Reply
You must be logged in to post a comment.